What is Porosity in Welding: Necessary Tips for Getting Flawless Welds
What is Porosity in Welding: Necessary Tips for Getting Flawless Welds
Blog Article
The Scientific Research Behind Porosity: A Comprehensive Guide for Welders and Fabricators
Comprehending the intricate systems behind porosity in welding is critical for welders and makers aiming for remarkable workmanship. From the structure of the base materials to the intricacies of the welding procedure itself, a wide variety of variables conspire to either intensify or minimize the visibility of porosity.
Understanding Porosity in Welding
FIRST SENTENCE:
Exam of porosity in welding exposes critical insights into the integrity and top quality of the weld joint. Porosity, identified by the visibility of tooth cavities or spaces within the weld steel, is an usual worry in welding procedures. These voids, otherwise effectively dealt with, can jeopardize the structural integrity and mechanical residential or commercial properties of the weld, resulting in prospective failures in the finished product.
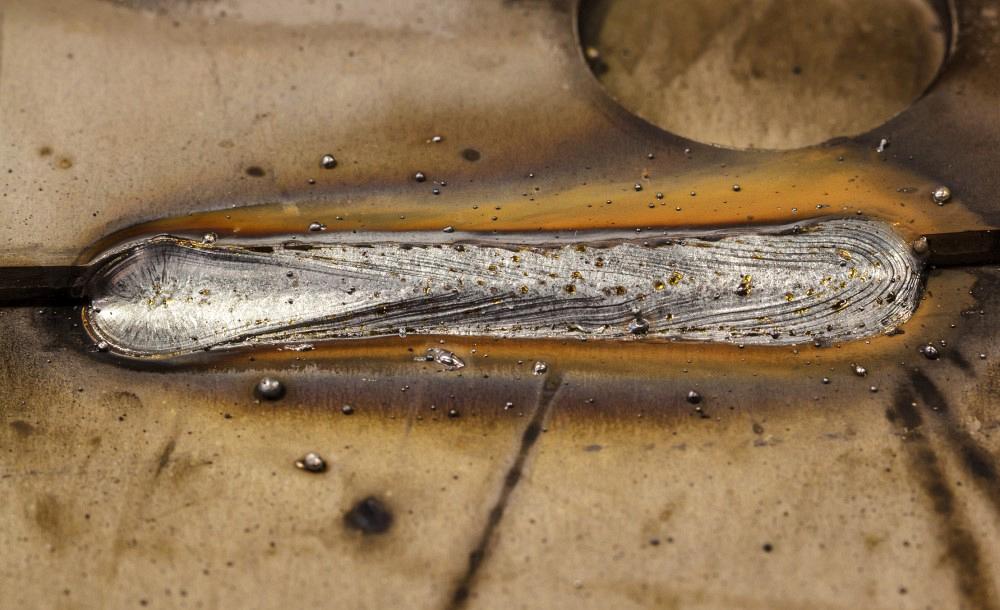
To discover and evaluate porosity, non-destructive testing methods such as ultrasonic testing or X-ray evaluation are typically employed. These methods permit the recognition of inner issues without jeopardizing the honesty of the weld. By assessing the size, form, and distribution of porosity within a weld, welders can make informed choices to improve their welding processes and accomplish sounder weld joints.
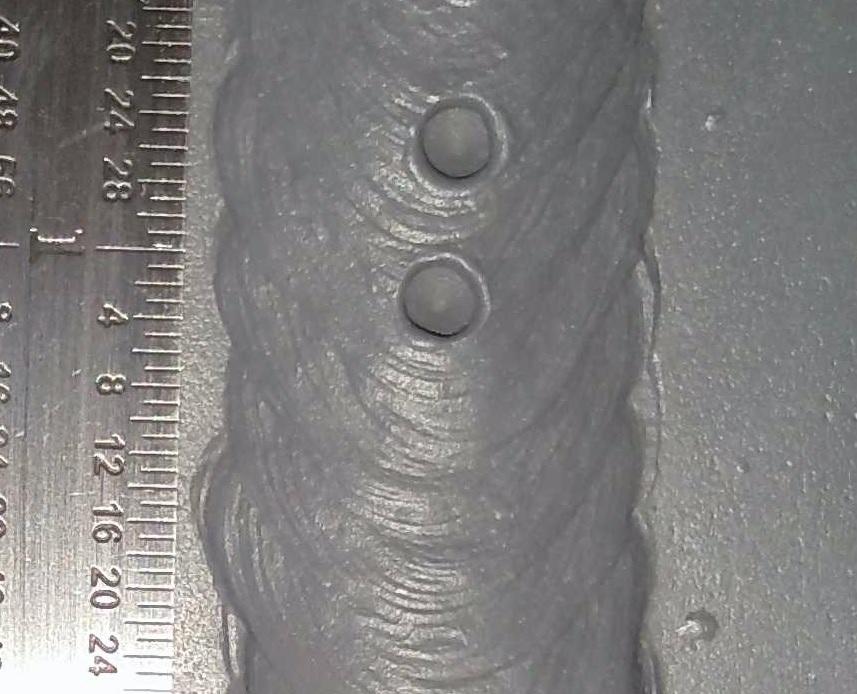
Aspects Affecting Porosity Formation
The event of porosity in welding is influenced by a myriad of variables, ranging from gas securing performance to the complexities of welding criterion setups. Welding criteria, consisting of voltage, current, take a trip rate, and electrode type, also impact porosity formation. The welding strategy used, such as gas steel arc welding (GMAW) or secured steel arc welding (SMAW), can influence porosity formation due to variations in warmth circulation and gas protection - What is Porosity.
Effects of Porosity on Weld Quality
Porosity development dramatically endangers the structural integrity and mechanical residential properties of welded joints. When porosity is present in a weld, look at more info it creates voids or dental caries within the material, reducing the total stamina of the joint. These voids serve as stress focus points, making the weld more prone to splitting and failure under load. The presence of porosity likewise deteriorates the weld's resistance to deterioration, as the entraped air or gases within the spaces can react with the surrounding setting, bring about destruction gradually. Furthermore, porosity can impede the weld's capability to withstand stress or influence, additional threatening the general top quality and dependability of the bonded framework. In crucial applications such as aerospace, automotive, or structural buildings, where safety and resilience are vital, the harmful results of porosity on weld high quality can have severe consequences, highlighting the significance of minimizing porosity with appropriate welding techniques and treatments.
Methods to Reduce Porosity
To improve the quality of welded joints and ensure architectural honesty, welders and makers utilize particular techniques focused on decreasing the formation of voids and dental caries within the product during the welding procedure. One reliable technique to reduce porosity is to guarantee proper you can try this out product preparation. This includes thorough cleansing of the base metal to get rid of any type of contaminants such as oil, oil, or wetness that could add to porosity formation. Additionally, making use of the suitable welding parameters, such as the right voltage, current, and take a trip speed, is crucial in preventing porosity. Preserving a consistent arc size and angle during welding additionally helps lower the probability of porosity.

Using the appropriate welding technique, such as back-stepping or employing a weaving movement, can also assist disperse warmth uniformly and reduce the possibilities of porosity formation. By carrying out these methods, welders can efficiently decrease porosity and create top quality bonded joints.
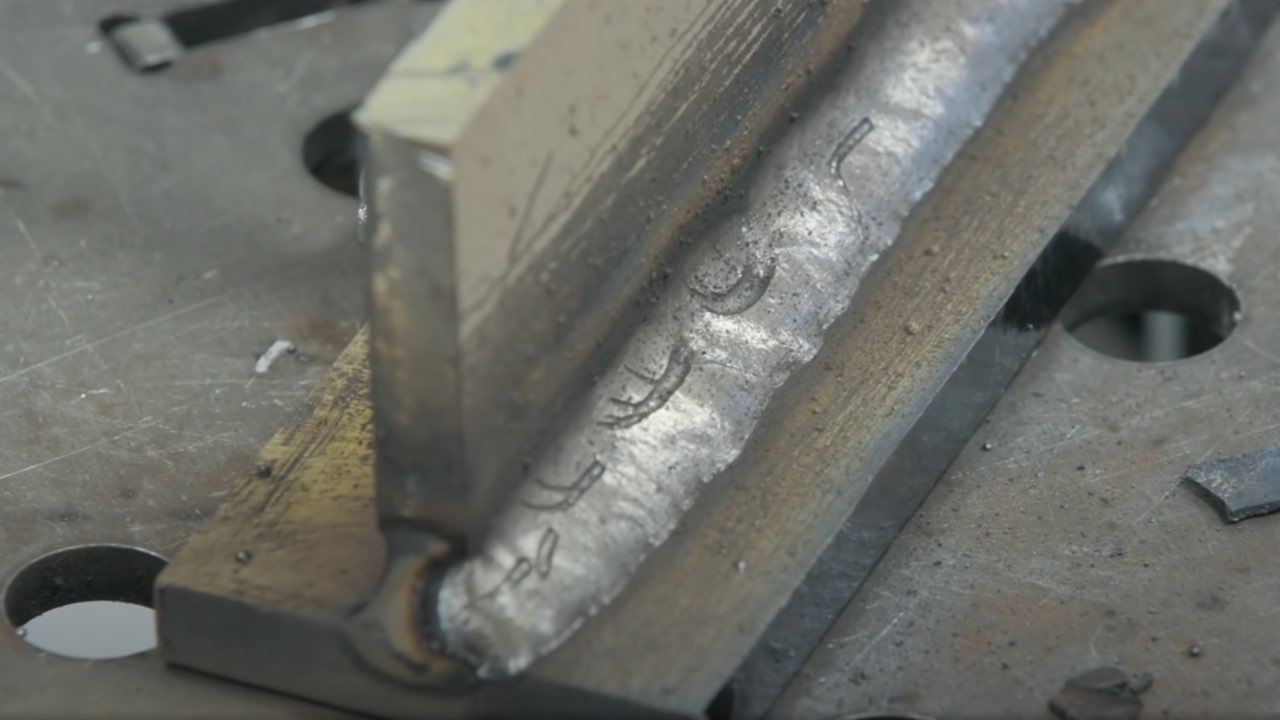
Advanced Solutions for Porosity Control
Applying innovative innovations and innovative approaches plays a pivotal duty click in attaining exceptional control over porosity in welding procedures. In addition, using sophisticated welding methods such as pulsed MIG welding or modified atmosphere welding can likewise assist reduce porosity issues.
An additional innovative solution entails making use of innovative welding tools. Using equipment with built-in functions like waveform control and advanced power resources can boost weld quality and reduce porosity threats. In addition, the application of automated welding systems with exact control over parameters can dramatically decrease porosity defects.
Additionally, including advanced surveillance and evaluation innovations such as real-time X-ray imaging or automated ultrasonic testing can help in detecting porosity early in the welding process, permitting immediate restorative activities. On the whole, incorporating these sophisticated options can significantly improve porosity control and boost the general top quality of bonded components.
Final Thought
In conclusion, recognizing the scientific research behind porosity in welding is crucial for welders and makers to produce premium welds - What is Porosity. Advanced services for porosity control can even more enhance the welding process and make certain a strong and trusted weld.
Report this page